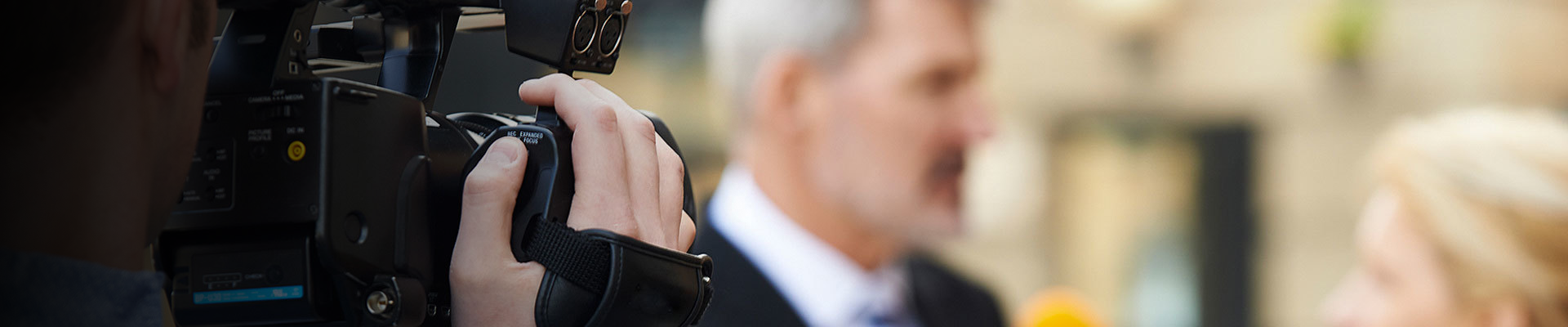
Blog
E-commerce logistics warehousing experience sharing
2021-09-02 10:14
E-commerce warehousing logistics is specially designed for e-commerce and fully meets the needs of e-commerce. Today Jiuwei to share with you someE-commerce warehousing logisticsSome dry goods in the process can avoid detours from small partners who do not know about e-commerce storage.
1, unified warehouse VS sub-warehouse, regional warehouse VS parallel warehouse
The so-called unified warehouse means that all orders are shipped from one warehouse. In contrast, warehouse splitting naturally means that multiple warehouses deliver goods at the same time.
There are two types of warehouses: regional warehouses and parallel warehouses. Except Amazon, the industry is almost all regional warehouses. For example, Shanghai warehouses send orders from Jiangsu, Zhejiang and Shanghai, while northern warehouses send parcels from the three eastern provinces. And parallel warehouse, in short, is which warehouse has the goods contained in the order, the order will be sent from where, when necessary, even to split the single multi-warehouse delivery, to achieve a highly automated order processing, less manual intervention, low requirements for operators; The disadvantage is that the system complexity is high, not everyone can do it.
For B2C with less than 2000 daily orders or densely distributed orders, unified warehouse is the only option. The reason is simple: if the daily outbound volume of a single warehouse is less than 1000 orders, fixed costs (rental property, general wages, management costs, utility network costs, amortization of fixed assets, etc.) are amortized to each order, especially in the first 3 years, the outbound cost greatly deviates from the industry's normal range of 6-9 yuan.
Unlike common sense, the biggest benefit of warehouse splitting is not the decline in average freight rates, although this is the main basis for most B2C companies' warehousing decisions. As far as my personal understanding is concerned, the existence of sub-warehouses greatly shortens the number of kilometers of transportation and indirectly reduces the package turnover rate of 3PL (third party logistics). Therefore, the loss of goods and the arrival time are both reduced, greatly improving the user experience. For B2C, which cannot build its own logistics and must rely on 3PL in the initial stage, it is a low-cost solution to improve the user experience, especially when the service quality of 3PL in China is generally not flattering.
What needs to be said is that the system of sub-warehouse is much more complicated than that of unified warehouse. It is necessary to reserve strong technical development force in advance and consider the underlying structure of the database in advance.
2. Warehouse plane layout
The function of e-commerce warehousing focuses on "passing" rather than "storage". In theory, the higher the turnover rate of goods, the better. The incoming quantity should be basically the same as the outgoing quantity, fast in and fast out. Based on the above functions, the function partitions of the warehouse are as follows:
A unloading/outbound platform
The platform, as the name implies, is a cement platform on the outside of the warehouse gate with the upper edge basically parallel to the lower edge of the vehicle box, which is convenient for personnel and the transfer vehicle directly enters and leaves the vehicle for unloading. Of course, for B2C whose daily stock-out volume is less than 1000 orders, whether there is a platform or not is not a big problem. Below the 3000 order, the unloading and delivery platforms can be shared. Of course, if your B2C inventory cycle is less than 10 days or even shorter, this account will have to be calculated separately (the industry generally controls it below 21 days).
B Receiving Area
The working areas of QC (if former QC) and receiving personnel are generally close to the gate. The supplier brings the PO form to this order, waits for QC and quantity inventory, and retrieves the stamped PO form as the receipt certificate.
C temporary storage area
Goods that have completed the warehousing process shall be pasted with corresponding labels, and the temporary storage area (whether to be QC or not, whether to be packaged) when waiting for shelves.
D storage area (common library, constant temperature library, valuable library)
According to the product characteristics and QC recommendations, in different storage shelves. Ordinary warehouses are divided into shelf areas and storage areas. Small goods are generally put on shelves, while large goods or goods with large/frequent delivery volume are generally directly placed on pallets to reduce unnecessary handling. Constant temperature storage placed on the temperature, humidity has certain requirements of the goods, especially cosmetics. Valuables warehouse is not much to say, everyone knows.
E Operation area
After the storage area has completed the transportation of the goods, it will be checked out of the warehouse, equipped with invoices, packed and pasted with waybills.
F Warehouse-out area
Check the quantity with the logistics company, scan and sign the handover place, which is also close to the gate.
3. Place PO Order & Pre-management
In warehousing practice, due to the great difference in the quality and cooperation of suppliers, warehousing is the upstream link with the lowest controllability and the most error-prone. Therefore, it is very important to manage PO orders and warehousing in advance. We often see the following problems:
A does not enter the warehouse according to the specified time or the amount of one-time storage is too large, and the platform is blocked.
B by express delivery, once the secondary packaging or outsourcing damage caused by shortage or damage, can not distinguish the responsible party, can only refuse to accept
C transport packaging does not meet the requirements, or no sales packaging (exposed goods), resulting in damage to the goods on the way or can not be normal shelves (easy to cause damage to the goods).
Considering that QC generally only does appearance QC and cannot cover 100, strict storage standards are formulated and the status of goods stored in advance is fully managed, which can avoid subsequent disputes (return of goods for quality problems, batch return to suppliers, etc.) at low cost and high efficiency, which is of great benefit to both suppliers and B2C.
4. QC & warehousing
On the premise of sufficient prior management, QC and warehousing will become relatively simple, and only the requirements of "PO Form" and "QC Instructions" need to be strictly observed. The reason why the vast majority of students feel that there are many problems in the warehousing process is not the problem of warehousing, but the failure of prior management.
The only thing worth mentioning is that if the incoming goods do not use international codes (that is, the kind used in large supermarkets), then pasting their own bar codes will become a huge workload. You know, this bar code needs to be affixed to every item. Generally large B2C, either print the label and transfer the workload to the supplier, or force the supplier to adopt the international code.
5, Storage Management
After QC and warehousing are completed, they will be put on shelves according to commodity characteristics. In addition to the three warehouses and two areas mentioned above, the basic principle of first-in, first-out, bottom-heavy and top-light should generally be observed. If the area is placed in parallel, the second-hand goods should be taken out first, and the new goods should be put in before finishing. For goods that require batch management (e. g. food with a short shelf life, fresh food, cosmetics; or where the purchase price fluctuates greatly and cost prices need to be calculated by batch accounting rather than dynamic weighting), different locations should be set up for different batches.
After setting up the location entry system for incoming goods, this link is completed.
6, picking, sorting, packing
Different from common sense and imagination, it is not sorting and packing that affects the efficiency most in the outbound link, but picking.
Picking, is the system according to a certain logic, the N orders contain sku summary to a picking list (also known as the catch list), by the warehouse group unified from the designated location to take out, to avoid each order to run to the warehouse area, improve the efficiency of the warehouse. For warehouses with large area and long distance between the three warehouses and the two areas, the picking list should be printed according to different storage areas and handed over to different commodity managers for picking.
Sorting is to allocate the goods listed on the picking list according to the details of the sorting list, with invoices and veneer sheets. Of course, there is also the most important link, the check of the outgoing bar code, and finally the necessary filling, internal packaging and packing.
What needs to be said is that WMS's deduction of physical inventory also occurs in the process of outbound inspection. The more advanced WMS also allows consumers to cancel or modify orders before going out for inspection.
Latest recommend
Contact Us
Headquarters Address: 1801, Floor 18, Building 6, Jiayue Plaza, Yard 9, Hongye Road, Daxing District, Beijing
Hotline:139-1033-6413
Contact E-mail:lixiulan@jwrack.com
Get in touch with our team in time and be happy to help you
COOKIES
Our website uses cookies and similar technologies to personalize the advertising shown to you and to help you get the best experience on our website. For more information, see our Privacy & Cookie Policy
COOKIES
Our website uses cookies and similar technologies to personalize the advertising shown to you and to help you get the best experience on our website. For more information, see our Privacy & Cookie Policy
These cookies are necessary for basic functions such as payment. Standard cookies cannot be turned off and do not store any of your information.
These cookies collect information, such as how many people are using our site or which pages are popular, to help us improve the customer experience. Turning these cookies off will mean we can't collect information to improve your experience.
These cookies enable the website to provide enhanced functionality and personalization. They may be set by us or by third-party providers whose services we have added to our pages. If you do not allow these cookies, some or all of these services may not function properly.
These cookies help us understand what you are interested in so that we can show you relevant advertising on other websites. Turning these cookies off will mean we are unable to show you any personalized advertising.